מלחמה ידועה כמנוע ההתקדמות הטוב ביותר. תעשיית הטנקים של ברית המועצות ביצעה קפיצת מדרגה איכותית מסחררת תוך שנים מלחמה בודדות בלבד. הכתר האמיתי של זה היה הטנקים מסדרת ה- IS.
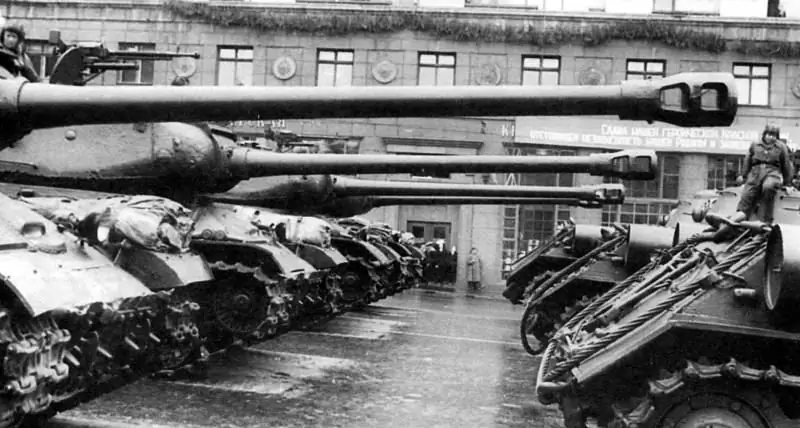
מתכוני מגניטוגורסק
בחלק הקודם של הסיפור, מדובר היה בשריון יצוק בעל קשיות גבוהה של 70 ליטר המשמש לצריחי טנקי ה- IS. מפתחי השריון מ- TsNII-48 היו רחוקים מהניסיון הראשון ביצירת הגנה על טנקים כבדים.
לפני בליטת קורסק, שהפכה לזרז לפיתוח בניית טנקים כבדים ביתית, המטרה העיקרית של המודרניזציה הייתה טנק ה- KV. בתחילה כל העבודות נועדו לצמצם את שיעור תוספי הסגסוגת הנדירים בהרכב השריון. אפילו השם ב- TsNII -48 העלה שם מתאים - פלדה מסגסוגת כלכלית. השריון המקורי של המותג FD-7954, שאיתו נכנס טנק ה- KV למלחמה הפטריוטית הגדולה, הכיל, על פי דרישות טכניות, עד 0.45% מוליבדן, 2.7% ניקל וכרום.
בסוף 1941, קבוצת חוקרים בראשות אנדריי סרגביץ 'זאבאלוב במכון המשוריין יצרה מתכון לפלדה FD -6633 או 49C, שבה המוליבדן דורש לא יותר מ -0.3%, כרום - עד 2.3%וניקל - עד 1, 5%. בהתחשב בכך שמכלים מסדרת KV מהמחצית השנייה של 1941 עד 1943 נאספו כ -4,000 עותקים, אפשר לדמיין את כמות החיסכון האמיתי במתכות מסגסוגות.
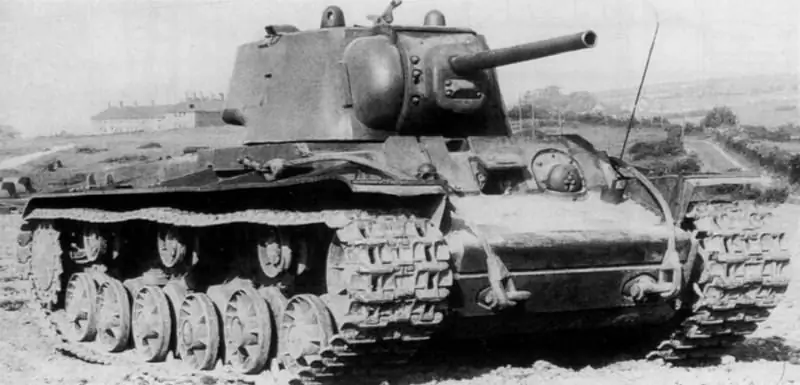
סוד ההצלחה
סוד ההצלחה של המטלורגים טמון בחקר הפרמטרים של היווצרות שבר סיבי של שריון - הפרמטר העיקרי של ההתנגדות לקליעים. התברר שאתה יכול להסתדר ללא חלק ניכר ממרכיבי הסגסוגת על ידי שינוי פשוט של קצב הקירור של השריון במהלך המרווה. אבל זה פשוט במילים - כמה ניסויים מקדימים והיתכות מטלורגיסטים היו צריכים לעשות, רק הארכיונים המסווגים כעת יוכלו לדעת.
במפעל המתכת ה Magnitogorsk בשנת 1941 התקבלו אב טיפוס הראשונים של פלדה 49C, שלא היו נחותים מהשריון המסורתי "שלפני המלחמה". בפרט, ההפגזה על ידי תותח 76 מ"מ הראתה עמידה מלאה בדרישות הטקטיות של הטנק. ומאז 1942, רק שריון עם השם 49C שימש לסדרת KV. ראוי לזכור כי צריכת הכרום, המוליבדן והניקל פחתה באופן משמעותי.
החיפוש אחר ניסוחים חדשים של שריון לציוד כבד לא הסתיים בכך. בשנת 1942 "מרותך" הפלדה GD-63-3, נטולת לחלוטין כרום וניקל. במידה מסוימת הוחלף הניקל במנגן - חלקו גדל יותר משלוש פעמים (עד 1.43%). אבות טיפוס לשריון החדש נורו. והתברר שהם מתאימים למדי לשימוש המוני בעיצוב ה- KV. אבל הטנקים של קלים וורושילוב עם שריון קשיחות בינונית פרשו. ואת מקומם של כלי רכב כבדים תפסו רכבי "יוסף סטלין" עם שריון בעל קשיות גבוהה.
שריון מגולגל 51C
אם ניתן היה להטיל את שריון ה -70 ליטר לצריח IS-2, הטריק הזה לא עבד עם חלקי גוף הטנק. כאן, המהנדסים התמודדו עם שתי בעיות בבת אחת - יצירת שריון בעל קשיות גבוהה בעובי רב והצורך לרתך אותו לתוך גוף סיים.
כל המתעניין כנראה כבר מודע לבעיות הנגרמות כתוצאה מריתוך של שריון T -34 - קיימת סבירות גבוהה להיסדק באזור הריתוכים. ה- IS-2 לא היה יוצא מן הכלל. וגופו היה אמור להתבשל במקור מחלקים שטופלו בחום.
כשהבינו אילו קשיים וסכנות פתרון טכנולוגי כזה יביא לפעולה צבאית, שינו מומחי TsNII-48 את מחזור ייצור הטנקים. כתוצאה מכך, בשנת 1943, במפעל בניית מכונות כבדות אוראל ובמפעל מס '200 בצ'ליאבינסק, הוחלט על גוף ה- IS-2 להתבשל מלוחות שריון שחלפו רק חופשה גבוהה לאחר גלגול. כלומר, למעשה, גוף הגוף של טנק כבד הורכב מפלדה "גולמית". זה הפחית מאוד את פגמי הריתוך בשריון המגולגל בעל קשיות גבוהה של 51C.
טיפול החום הסופי על ידי חימום לפני כיבוי בוצע כבר על גוף הטנק המרותך, לאחר שחיזק אותו בעבר בעזרת תמוכות פנימיות. הגופה הוחזקה בתנור במשך שלוש שעות. ואז, במכשירים מיוחדים, הם הועברו למיכל מרווה מים ושמרו בו במשך 15 דקות. יתר על כן, טמפרטורת המים במיכל המרווה עלתה מ -30 ל -55 מעלות צלזיוס. טמפרטורת פני השטח של הגוף לאחר הוצאתו מהמים הייתה 100-150 מעלות צלזיוס. וזה לא הכל.
לאחר המרווה, הגוף היה נתון מיד לרגיעה נמוכה בכבשן במחזור החום בטמפרטורה של 280-320 מעלות צלזיוס עם החזקה לאחר שהגיע לטמפרטורה זו במשך 10-12 שעות. הרפיה נמוכה של מגדלים יצוקים משריון 70L בוצעה בצורה דומה. מעניין לציין כי בקרת הסדקים בגופי ה- IS-2 הניסיוניים נמשכה ארבעה חודשים, כאשר מכלי הייצור הראשונים יצאו משערי המפעל.
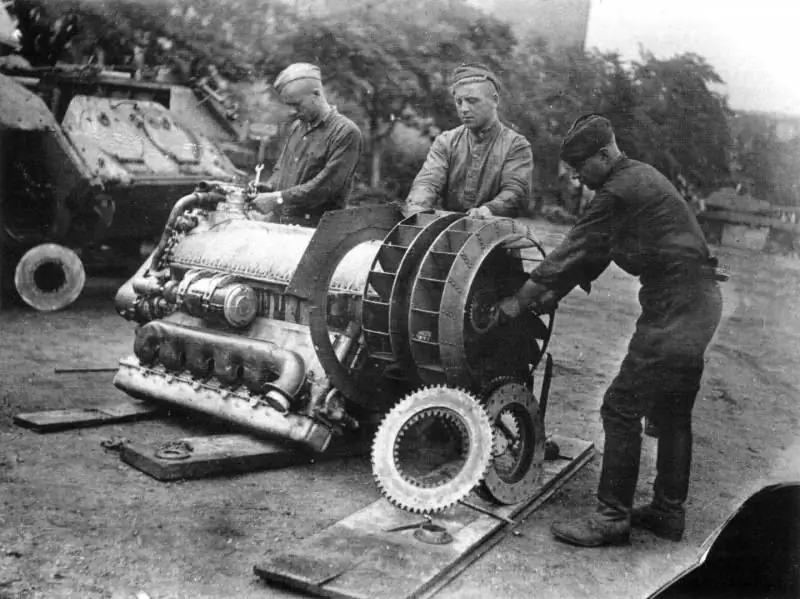
תרכובת כימית
מה היה השריון המגולגל 51C שהפך להיות העיקרי עבור ה- IS-2, ISU-122 ו- ISU-152? זוהי פלדה מתקשה לעובי עובי שריון גדולים עם ההרכב הכימי הבא (%):
C 0, 18-0, 24
Mn 0, 70-1, 0
סי 1, 20-1, 60
Cr 1, 0-1, 5
Ni 3.0-3.8
מו 0, 20-0, 40
P ≤0.035
S ≤0.035.
בהשוואה לשריון יצוק 70L, לפלדה המגולגלת 51C היה שיעור גבוה יותר של מוליבדן וניקל, מה שהבטיח עלייה בקשיחות עד 200 מ"מ. כאשר גוף הטנקים הכבדים נורו עם פגזים של 88 מ"מ, התברר כי השריון בעל קשיות גבוהה עדיף בהרבה בעמידות על קודמיו הקשיחים הבינוניים. סוגיית הצבת שריון מגולגל 51C נפתרה באופן מיידי.
ריתוך חכם
תרומה חשובה להצלחת פיתוח ייצור השריון של טנקים מסדרת ה- IS נעשתה על ידי ריתוך פלדה אוטומטי מתחת לשכבת שטף. מכיוון שלא ניתן היה להעביר את כל תהליך הייצור של גוף משוריין טנק לריתוך כזה בתחילת 1944, התמקדו המהנדסים באוטומציה של התפרים המורחבים והעומסים מכנית ביותר.
במפעל מס '200 בצ'ליאבינסק, בתהליך הרכבת גוף הגוף של הטנק הכבד IS-2, ניתן היה לבצע אוטומציה של רק 25% מכלל הריתוכים. באמצע 1944 הצליח טנקוגראד לבצע אוטומציה של 18% מכל 25% הריתוכים האפשריים. האורך הכולל של התפרים המרותכים לאורך גוף הטנק הכבד IS-2 היה 410 מטרים רצים, מתוכם 80 מטר ריצה בוצעו בשיטת הריתוך האוטומטית.
תוצאה זו הביאה לחיסכון משמעותי במשאבים וחשמל נדירים. ניתן היה לשחרר עד 50 ריתוכים ידניים מוסמכים (עלויות העבודה שלהם בסך 15,400 שעות עבודה) ולחסוך 48,000 קילוואט שעות חשמל. ירידה בצריכה של אלקטרודות (כ -20,000 ק"ג, אוסטניטית - 6,000 ק"ג), חמצן (ב -1,440 קוב).
גם הזמן שהוקדש לריתוך צומצם משמעותית. לדוגמה, ריתוך קופסת התחתונה והצריח לצדדים בתפר של שישה עשר מטרים לקח 9.5 שעות עבודה במצב ידני, ורק 2. תפר דומה באורך המחבר את החלק התחתון לדפנות גוף הטנק במצב אוטומטי נדרש. 3 שעות עבודה (במדריך מיידי 11, 4). במקביל, ניתן היה להחליף רתכים מיומנים במיוחד בעובדים לא מיומנים בריתוך אוטומטי.
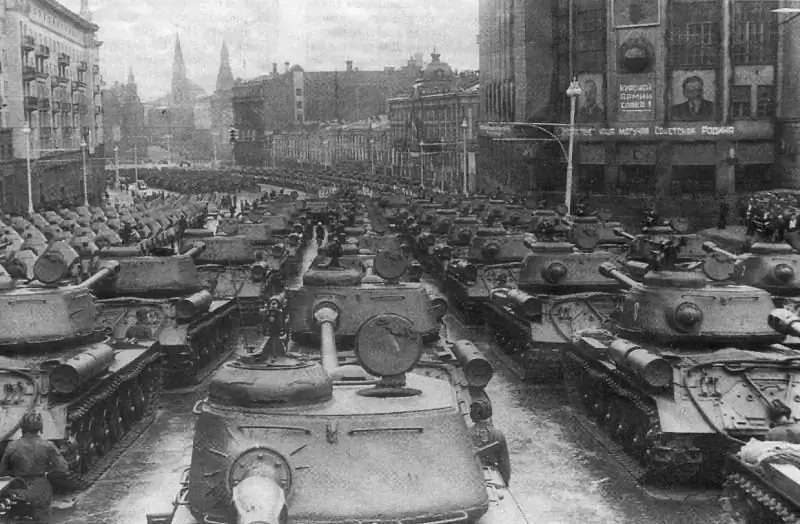
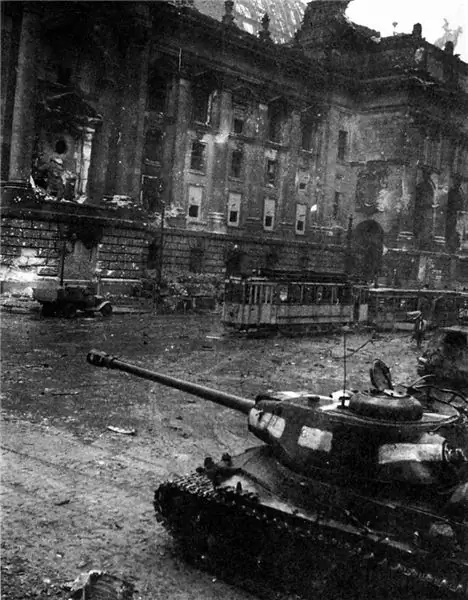
סוכנויות אוראל
חוקר תעשיית הטנקים הסובייטים, מועמד למדעי ההיסטוריה זאפרי וסילי ולדימירוביץ 'מהמכון להיסטוריה וארכיאולוגיה של ענף אוראל באקדמיה הרוסית למדעים באחת מיצירותיו מתאר בפירוט רב את יחידות הריתוך האוטומטיות המשמשות באוראל לשריון. ייצור גוף.
הנפוץ ביותר היה רובה סער מסוג "ACC" עם ראש בשטדט. היו באורלמאש שמונה מתקנים כאלה. מהירות הזנת החוטים במכונה זו הייתה תלויה במתח בקשת. הוא דרש 5 יחידות, כולל 3 מנועים חשמליים קינמטיים וגנרטור אחד.
באמצע 1943, מכונת הריתוך SA-1000 תוכננה לצרכי הטנקים הכבדים IS-2. או מכונת ריתוך בקיבולת של עד 1000 A.
על מנת לשלוט בייצור גוף משוריין עבור הטנק הכבד החדש צ'ליאבינסק IS-3, תכננו מהנדסי המפעל בשנת 1944 את המכשיר "SG-2000". מכונה זו תוכננה לעבודה עם חוטי ריתוך דלי פחמן בקוטר מוגדל (6-8 מ"מ) ומצאה את יישומה בייצור מגדל IS-3. במתקן היה מתקן להכנסת הרכב מיוחד (סגסוגות ברזל שונות) לחלק הריתוך על מנת להסיר (לשחזר) את המתכת בו. בסך הכל, על פי העיקרון של ויסות עצמי של קשת הריתוך ב- UZTM, בשנת 1945, נוצרו 9 מתקני ריתוך אוטומטי משלושה סוגים: "SA-1000", "SG-2000", "SAG" ("ריתוך אוטומטי" רֹאשׁ").
יפה יותר משריון גרמני
התוצאה של כל הסיפור עם השריון של טנקים כבדים של דאעש הייתה פיתוח מהיר להפתיע של מתכון פלדה שעלה על שריון גרמני בתכונות הטקטיות שלו. TsNII-48 קיבל פלדה הניתנת להקשה 120 מ"מ, שעובדה ניתן במידת הצורך לעלות ל 200 מ"מ.
זה הפך להיות הבסיס העיקרי לפיתוח המשפחה של הטנקים הסובייטיים הכבדים שלאחר המלחמה.